Acoustic Power Transfer (APT) can be used to wirelessly power implantable devices. Most of these devices use batteries as a power source. However, batteries need to be replaced every so often resulting in a surgery, and therefore, they are not an appropriate candidate for long-term powering purposes. Furthermore, efforts to reduce device size now require focus on a suitable replacement for batteries, as battery technology has not kept pace with ever-shrinking modern electronics. Acoustic power transfer through human tissue is orders of magnitude more efficient than other wireless powering methods such as electromagnetic (EM) or radio frequency (RF) at small sizes (less than a few mm) and large implant depths (greater than 1 cm). The goal of this project is to enable a new mode for power transfer to deeply implanted biosensors using standard ultrasonic imaging equipment. An external ultrasonic transmitter converts electrical energy into a pressure wave which is transferred through the body tissue. The pressure wave is captured by a receiver implanted in the body, and converted to electrical energy by an inverse process. A rectifier provides a usable stable DC voltage for powering a bio-sensor.
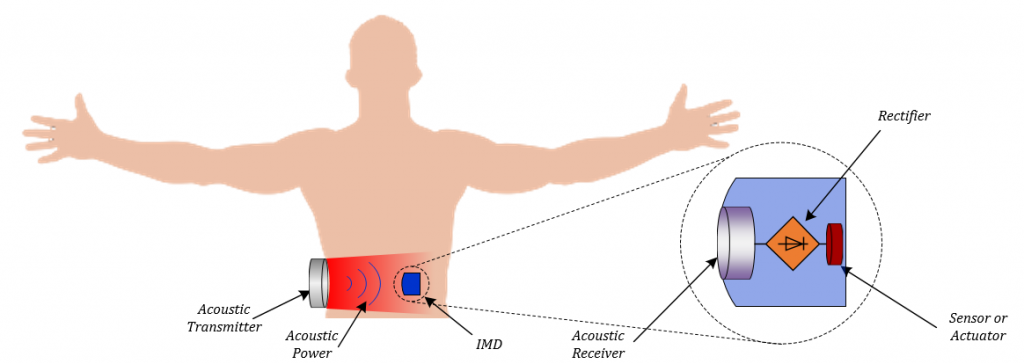
We are studying the potential of using acoustics along with piezoelectric MEMS receivers / generators to deliver power to deeply implanted bio-devices (i.e. glucose sensors, pressure sensors, targeted drug delivery systems, metabolic sensors, etc.). After undertaking basic studies to understand the relationships between power transfer and micro-scale receiver design for two common receiver architectures, i.e. plate and diaphragm, we found that for generator diameters in the sub-millimeter range, the diaphragm generally generates more power than the plate and is significantly less sensitive to changes in implant depth. Therefore, we are now developing a micromachined ultrasonic power generating receiver with a size of less than 1cm×1cm capable of providing sufficient power for implantable medical devices. The ultrasound receiver takes the form of a unimorph diaphragm consisting of PZT on silicon.
Researchers
David Christensen
Hamid Basaeri
Publications
- Basaeri, H., Christensen, D., Roundy, S., 2016. “A Review of Acoustic Power Transfer for Bio-Medical Implants”, Smart Materials and Structures. 25.12 (2016): 123001. [link]
- Yu, Y., Nguyen, T., Tathireddy, P., Roundy, S., and Young, D.J. 2016. “Wireless Hydrogel-Based Glucose Sensor For Future Implantable Applications”, IEEE Sensors, Oct. 30 – Nov. 2, 2016, Orlando, FL.
- Basaeri, H., Christensen, D., and Roundy, S. 2016. “Ultrasonically Powered Hydrogel-Based Wireless Implantable Glucose Sensor”, IEEE Sensors, Oct. 30 – Nov. 2, 2016, Orlando, FL.
- Yu, Y., Bhola, V., Tathireddy, S., Roundy, S., Young, D. 2015. “Inductive Sensing Technique For Low Power Implantable Hydrogel-Based Biochemical Sensors”. SENSORS, 2015 IEEE. IEEE, 2015. [link]
- Christensen, D., Roundy, S., 2015. “Ultrasonically powered piezoelectric generators for bio-implantable sensors: Plate versus diaphragm.” Journal of Intelligent Material Systems and Structures (2015): 27.8 (2016): 1092-1105. [link]
- Christensen, D., Roundy, S., 2013. “Comparative Study of Bio-implantable Acoustic Generator Architectures”, Technical Digest PowerMEMS 2013 (London, UK, 4-6 December 2013) pp. 638-687. [link]
Sponsors